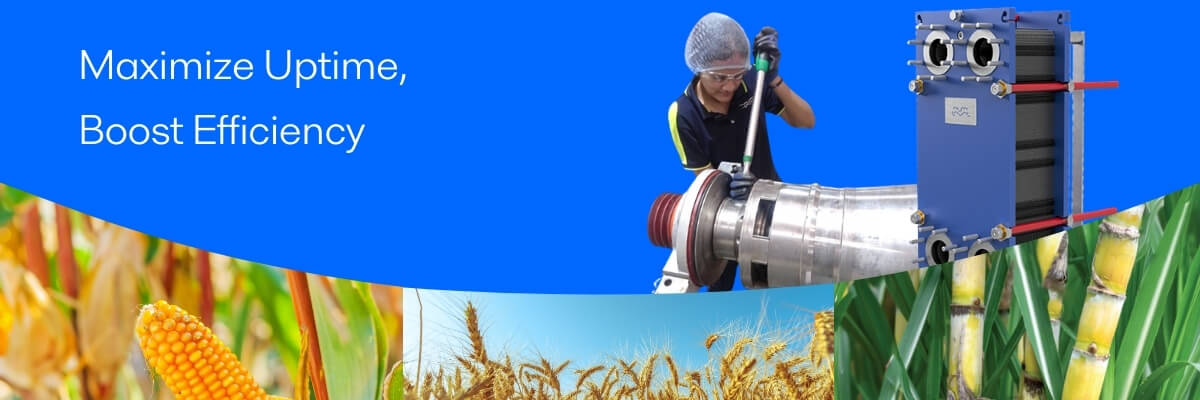
Services tailored to your ethanol production needs
Maximize Uptime with Tailored Ethanol Service Solutions Every ethanol plant operator aims for maximum efficiency and uninterrupted operations. Alfa Laval’s 360° Service Portfolio ensures your equipment runs at peak performance throughout its lifecycle—from start-up and maintenance to optimization and monitoring. Our customized service agreements help you reduce unplanned downtime, optimize costs, and extend equipment life. Not on a Service Agreement? Your First Inspection & Consultation Is on Us! Get expert insights into your equipment’s health at no cost—because prevention is better than downtime!
Comprehensive Service Agreement – Total Care for Your Decanter
A complete maintenance package covering both scheduled and unscheduled service needs.
This includes:
- Planned preventive maintenance & breakdown support
- Most parts covered (excluding bowl, frame, instrumentation & lubricants)
- Critical spare parts included (kits, bearings, bearing housings & hubs)
- Fixed number of conveyor refurbishments
Bundled Service Agreement – Keep Your Decanters & Heat Exchangers at Peak Performance
A specialized service package that ensures routine health checks for your Decanters and Plate Heat Exchangers, helping you plan production and shutdowns efficiently.
This includes:
- Proactive insights with visit & audit reports
- Timely delivery of consumables and spares
- Exclusive stock of kits and wear parts for minimal downtime
- Quick conveyor replacement with ready-to-exchange units
Remote Guidance Services – Expert Support Anytime, Anywhere
Stay connected with virtual troubleshooting and monitoring for seamless operation.
This includes:
- Live remote support for troubleshooting & inspections
- Connectivity hardware & software for real-time monitoring
- Expert assistance in integrating your decanter controller
Exclusive 30-Min Remote Support – Got a Question? Ask Us!
Need quick troubleshooting or expert guidance? Get 30 minutes of free remote support—just WhatsApp us and we’ll take care of the rest!
Connect now via WhatsApp for a 30-min equipment inspection!
Conveyor Exchange Programme – Minimize Downtime with Ready-to-Use Refurbished Units
No more waiting for repairs—swap your damaged conveyor with a refurbished unit from our ready stock.
This ensures:
- Faster delivery & reduced lead time
- Readily available tiled conveyors for grain-based distilleries
- Quick support to keep your operations running smoothly
Scope of Service Agreement
The scope of the Service Agreement covers parts required for preventive maintenance and service visits.
It includes:
- Scheduled visits for performing periodic maintenance, such as health inspections and major servicing of decanter centrifuges
Energy Audit Lite – Optimize Heat Exchanger Efficiency
Looking to cut energy costs? Our Energy Audit Lite provides key insights on your heat exchanger performance, helping you reduce energy consumption and optimize efficiency.
Contact Us
Contact us and we’ll take care of the rest! | Hotline Number: +91-96589 71971 | WhatsApp Number: +91-97666 64726 | Email: india.info@alfalaval.com