How Alfa Laval is still the cream of the crop when it comes to Dairy
The origins of Alfa Laval are steeped in milk. When Gustaf de Laval and his partner Oscar Lamm launched the world’s first continuous separator for the Dairy industry in 1890, they were creating an organization that would grow into a multi-sector global provider of heat transfer, separation and fluid handling solutions with a strong focus on water-saving and energy efficiency.
DATE 2025-04-03It is a history of which to be proud, but no matter how broad Alfa Laval’s expertise has developed, milk is still running through the veins, and the innovation and pioneering spirit that launched the business more than 140 years ago is still driving the company’s Dairy business unit forward today and keeping it ahead of the pack particularly when it comes to sustainability-driven innovation.
It is a passion that burns bright in Jakob Worsoe, Senior Global Key Account Manager for TetraPak at Alfa Laval and the lead on all things Dairy.
“We certainly have a proud heritage to build on – and we have never lost that spirit of innovation,” he says. “We were the inventor of the dairy separator, and we also claim the first gasketed plate pasteurizer, although I believe there is always some debate about that one!
“These inventions were revolutionary at the time, and although the drivers may change, we are still inventing and reinventing our technology to meet the ambitions of our customers.
“Back at the start, it was quite fundamental as people could die if the milk hadn’t been treated properly; then, for many years, the big driver was improving the process to treat milk more cheaply. Today, our customers have other drivers: they want technology that boosts their sustainability and saves on water, energy and CO2 emissions, and we are not only delivering on that, but we also share those values and ambitions ourselves.”
Decades of Alfa Laval’s expertise can be seen in how the separator has evolved from the original model.
“The process of separating used to be a manual job,” explains Jakob. “Now we have the most efficient separators in the world, using the lowest amount of power. “Alfa Laval separators are uniquely designed to prevent air from entering, allowing milk to separate gently with minimal physical resistance. This design not only preserves the quality of the milk but also enhances energy efficiency. Additionally, by eliminating air friction outside the bowl, we achieve further energy savings.”
The evolution of the plates used in Alfa Laval’s heat exchangers for the Dairy industry over the years is another example of the technological drive towards compactness and efficiency. The first models used plates of 1cm in thickness, and over the decades of optimization, the plates have now been 0.5mm.
So just as it was in the 1880s, it is Alfa Laval leading the way when it comes to advancing technologies and reinventing and inventing processes.
“It is Alfa Laval that is defining the challenges and delivering the sustainable products and solutions to meet our customers’ requirements – in Dairy and all the other industries we work in,” says Jakob.
Looking forward to the next generation of products, Jakob highlights a new generation of agitators which will be launched during the year, another game-changer.
“We looked at how customers were carrying out their maintenance of the tanks, and it was basically an eight-hour job for two people. With this agitator, we have come up with a solution that will take one person less than 30 minutes. That is a massive boost in terms of labour saved and the downtime of the tank – but also, of course, represents savings on energy and water consumption in the use face, which is exactly what customers are looking for now.”
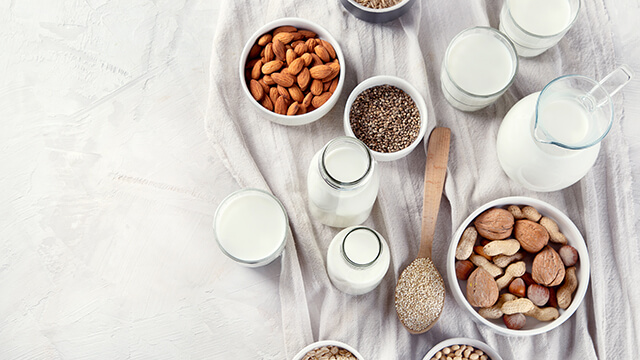
In the Dairy industry globally, Jakob sees key geographical themes emerging, all of which can be supported by Alfa Laval technology. In Europe and the US, for example, milk consumption is dropping slightly, so dairies are looking to diversify and move into the manufacturing of products such as butter, cheese and whey protein.
“Whey proteins are a super-hot trend at the moment,” says Jakob. “It used to be fed to pigs but these days, this is where the value is and it can be sold to drinks and food producers for use in energy drinks, supplements and protein bars.”
Meanwhile, in many Asian countries, particularly India and Pakistan, there is less milk being processed – about 35% -- with the rest going straight from cow to mouth, so there is a drive here to increase dairy production as a safe and healthy part of the national diet as it is rich in vitamins, proteins and fat.
But wherever the milk is being produced, Jakob believes the drive towards more sustainable operating – especially with water-saving – is unstoppable, and Alfa Laval is ahead of the field when it comes to delivering this and the ultimate cost savings that follow.
“We know our products are not always the cheapest, but they are superior, and the investment up front will deliver significant savings down the line for our customers,” he says. “This is so close to my heart that we all make the right decisions about the environment. At Alfa Laval, we don’t accept new products that use more energy, water and resources, and everything we have produced in the last 10 years really brings something to the table in terms of sustainability.”
As for the future, Jakob is looking forward to further innovations, which will be as game-changing now as the continuous separator was back in 1890. Technology that saves on water is at the top of the list.
He says: “Currently you cannot always re-use water within the process but I am sure that will change because we can clean the water to such a high degree – and that will particularly help in water-scarce regions and could even make the dairies water positive, which would be fantastic. We have all the technologies to make this a reality.”
Alongside the drive for sustainability comes the basic need to fill the protein gap in the future and keep a growing global population fed,
“I am an optimistic person,” says Jakob. “We need to feed the world, and dairy products will always play a part in that. Plant-based alternatives also have a role to play. There is no point in dairy fighting against plant-based processing – they can work side by side.
“In fact, they have the same challenges with water use, and most of the equipment is more or less the same, so they can learn from each other, and our position in both fields puts us in the ideal position to support both.”
Jakob Worsoe, Senior Global Key Account Manager
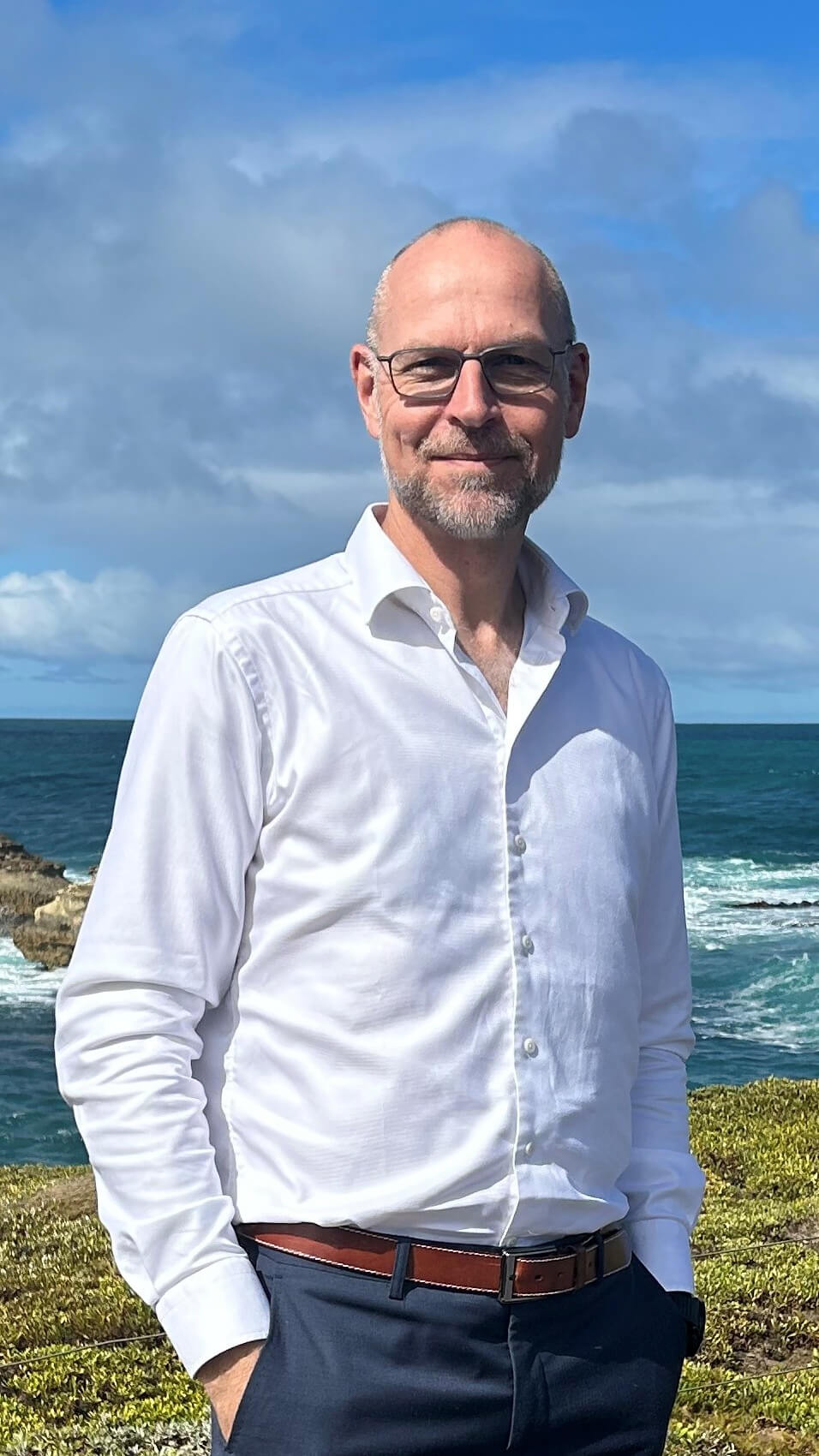
Highlighted industry: Dairy processing
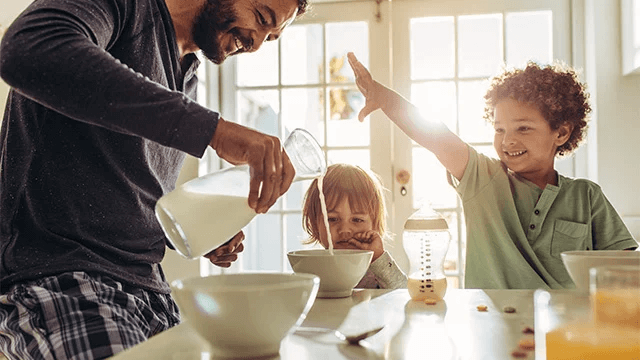
Driven by continuous innovation for over a century, Alfa Laval provides dairy processing equipment that maximizes yield, facilitates easy cleaning, and minimizes waste at every step. Our components help you save on water, energy, and chemicals while meeting the strictest safety and hygiene standards. This way, dairies can make the most of every resource and create top-quality dairy products – with the flexibility and confidence to seize new opportunities in the market.