Indirect heating and cooling in the chemical industry, Deccan Fine Chemicals
With Alfa Laval T series plate heat exchangers in their reactors, Deccan Fine Chemicals could optimize the temperature of all their batch processes without having to worry about costly shutdowns or maintenance from fouling.
DATE 2025-06-04This solution made it possible for them to use less fresh water and glycol. So, it is no surprise that Alfa Laval will continue to supply gasketed plate heat exchangers for their new expansion projects.
Deccan Fine Chemicals Ltd (“Deccan”) is a privately owned, global company in Tuni, Andhra Pradesh, India. It is jointly owned by Mitsubishi Corporation (Japan), Belchim Management (Belgium), and Indian partners. They focus on the custom manufacturing of active ingredients and advanced intermediates for leading crop protection, pharmaceutical, and specialty chemical companies in the USA, Europe, Asia, and South America.
Growth and expansion for Deccan
As a growing company, Deccan was planning a large-scale expansion for their facility in Tuni, India to be able cope with increasing capacity. This would include new reactors, each needing three heat exchangers for heating, cooling and chilling purposes. Due to the range of specialised products produced, these reactors would need to adjust to the optimum conditions of each product under production. Traditionally this would have been achieved using a direct heating system where steam, cooling water, or brine (glycol) would be applied in a heating and cooling jacket. This can be a simple and effective solution if you are managing static processes that operate under steady conditions, but for batch operations like Deccan’s, this would come with noticeable setbacks like:
- Heavy thermal inertia
- Sudden thermal expansion and contraction effects
- Scaling and fouling issues in the jacket
- Poor thermal efficiency
- Thermally inflexible
- Cleaning difficulties
- Corrosion sensitivity
- Temperature control difficulties
Instead, Deccan would need to find a solution that could fit the flexibility needs of their customization services in their new expansion. So, a pilot project was initiated to evaluate the best technical solution for the new footprint.
The solution - state-of-the-art closed loop
To fit the specific requirements of this new expansion, a state-of-the-art closed loop heating and cooling solutions would be the perfect fit. As a closed loop is either heated or cooled using separate heat exchangers, each one can be optimized for a particular duty. In Deccan’s case, they could use one heat exchanger for providing heat from steam, one for cooling with water or glycol, and one for chilled brine to ensure the temperature flexibility they needed. On top of that, this new solution comes with many extra benefits like:
- High energy efficiency
- Fewer CO2 emissions
- Better product spec
- Better process and temperature control (1°C)
- Flexible production
- Increased reactor lifetime
- Lower water consumption
- Lower effluent load
- Self-regulating glycol control
- Better safety
- Better Capex
Providing a product that is tailor made to fit a customer’s specifications is what we are best at, so working with a company that can do the same for us is paramount. With Alfa Laval, we didn’t have to pick between performance, cost, or energy efficiency because they found a solution that is made for our operation.
Mr.KVLP Raju
Director Technical at Deccan Fine Chemicals in Tuni
This solution, while better suited to their processes, comes with a design challenge due to the asymmetrical nature of Deccan’s duties. Asymmetry is challenging to work with because it means that the flow will not be equal between the hot and cold side of the heat exchangers. This reduces heat transfer efficiency and increases the risk of fouling in the heat exchanger. With over 500 Alfa Laval units already installed at the site, Deccan could trust us to supply a reliable and high-quality solution. We presented our new Alfa Laval T-series, a line of gasketed plate heat exchangers that can be both symmetrical & asymmetrical depending on the application.
In our asymmetrical design, narrow channels are fitted to the smaller flow and wider channels are fitted to the lager flow. This ensures that the velocity and turbulence is at the same level, minimizing the risk of fouling and bypassing the main disadvantage of the selected innovative reactor temperature control approach. Deccan was so happy with our proposal that they decided to install 20 Alfa Laval T10-B and T10-M units in the pilot project. The success of Alfa Laval plate heat exchangers in the pilot has meant that we will be supplying all 1000 units to the expansion.
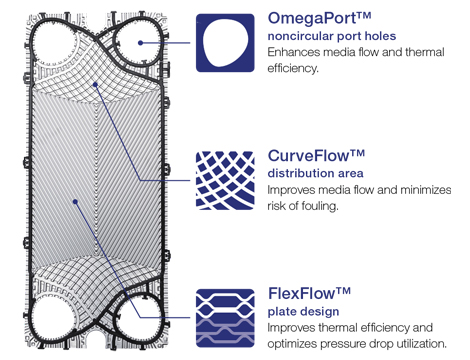
Products
T10-B and T10-M units at Deccan Fine Chemical’s Tuni site for the first phase in an expansion project.
Benefits of using Alfa Laval T-series for reactor heating and cooling
- Asymmetrical channel design
- Utilize available pressure drop
- Reduced risk of fouling
- Optimized heat transfer
- Reduced Capex